На предприятиях с использованием токарных станков одной из ключевых задач является увеличение их производительности. Однако ручная установка заготовки и последующее удаление ее остатков после обработки требует значительных временных затрат, что снижает общий темп производства. Данный вопрос особенно актуален при серийном выпуске продукции. В этом случае применяют автоматизированные устройства — барфидеры, которые заменяют ручную загрузку и выгрузку прутков. В новой статье расскажем о принципе работы и преимуществах барфидеров, как они помогают оптимизировать производственный процесс.
Благодаря передовым технологиям металлообработки процесс производства значительно оптимизировался и масштабировался. Современные токарные станки с ЧПУ отличаются удобным управлением, позволяют добиться высокой точности обработки.
Однако по-прежнему остаются некоторые сложности с точки зрения автоматизации. Закрепление заготовки на станке, удаление готовой детали после обработки требует определенного времени. Это отвлекает оператора от других задач и сказывается на общей эффективности, даже если работу выполняет опытный специалист.
Одним из решений такой задачи для токарных станков стало использование барфидеров — устройств, которые автоматически подают заготовки, извлекают остаток старого прутка после обработки и загружают новые.
Как работает барфидер, его основные параметры
Автоподатчик прутка имеет собственный шкаф управления и оснащен промышленным контроллером. В большинстве моделей имеется выносной пульт управления, на котором расположены: переключатели ручного и автоматического режимов, кнопка аварийной остановки, перевод из режима подачи в режим загрузки.
Прутки загружают в накопитель, который заранее настраивают под определенный угол наклона, длину, диаметр и форму заготовки. Податчик переводят в положение первой подачи, он перемещает пруток в рабочую зону станка и отъезжает обратно. Длину подачи регулируют с помощью упора.
Заготовку фиксируют зажимным устройством (приемной цангой) на оси вращения. Толкатель по заданной программе проталкивает пруток через сквозное отверстие шпинделя в зону обработки. Чтобы не возникало подклиниваний во время прохождения, пруток должен быть с фаской и без заусенцев. Для снижения вибрации из-за возможной кривизны заготовки в направляющие каналы подают гидравлическое масло.
Загрузчик отъезжает в исходное положение, срабатывает режим податчика. По завершении цикла обработки податчик выталкивает остаток прутка, возвращается в исходную позицию и переходит в режим загрузки нового.
Управляющие системы станка и барфидера синхронизируют и настраивают таким образом, чтобы обеспечить точное позиционирование. Это предотвращает биение заготовки в шпинделе, которое может привести к повреждению и поломке инструмента, браку выпускаемой продукции.
После корректной настройки работа идет в автоматическом режиме по заданному алгоритму без непосредственного участия оператора. Система сама устанавливает заготовку, а инструмент обрабатывает по выбранным параметрам. Как только деталь полностью обработана, барфидер заменяет ее новой заготовкой.
Оператор регулирует накопитель, лоток и податчик по уровню для корректной работы. Следит за состоянием рабочего инструмента, контролирует процесс смены прутков, их наличие в накопителе, вовремя загружает дополнительные. Специалист периодически проверяет качество готовых изделий.
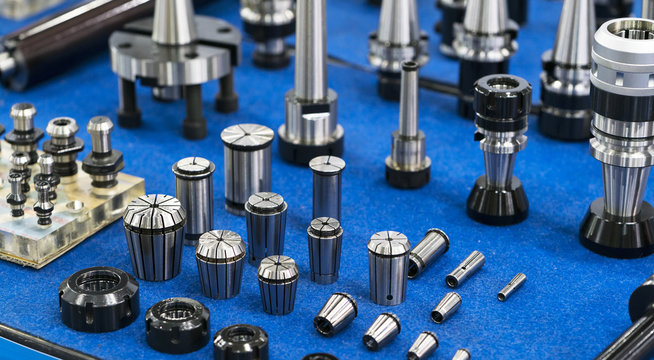
Ключевые параметры настройки:
- диаметр прутка, крутящий момент, показатель смещения;
- длина детали, расстояние подачи и торможения, характеристика отрезного инструмента (чтобы барфидер рассчитал количество изделий, которые можно сделать из прутка);
- скорость подачи и смена прутка, количество заготовок в накопителе;
- качество верхней обработки, чтобы резец отрезал конец прутка и получился ровный торец;
- уровень давления, настройка виброгасителей и упоров;
- настройка первой подачи толкателем;
- задержка закрытия патрона;
- состояние холостого хода;
- передний упор в ручном режиме;
- время зажима;
- параметры безопасности, вспомогательные сигналы.
Виды барфидеров для токарного станка
Подающие устройства условно разделяют на несколько категорий, которые отличаются по максимальной длине и диаметру загружаемых прутков. Их форма может быть круглой, квадратной, шестигранной или сложной. Под каждую конфигурацию используют определенный тип зажимных цанг и модель подающего механизма.
В металлообработке применяют прутки из алюминия, меди, бронзы, латуни, других металлов и сплавов. Наиболее востребованные заготовки имеют длину от 0,5 до 4 метров, диаметр — от 0,03 до 0,7 метра.
Напомним, что классификация барфидеров условная, у каждого производителя свои требования к оборудованию и параметрам заготовок. В зависимости от конкретной модели бывают устройства для подачи:
- длинных и тонких заготовок, длина которых составляет от 1500 до 4000 мм, а диаметр — от 3 до 25–30 мм;
- широких заготовок диаметром от 30 до 65 мм и длиной от 250 до 1500 мм. Чтобы использовать более длинные прутки, нужны дополнительные устройства для выправления.
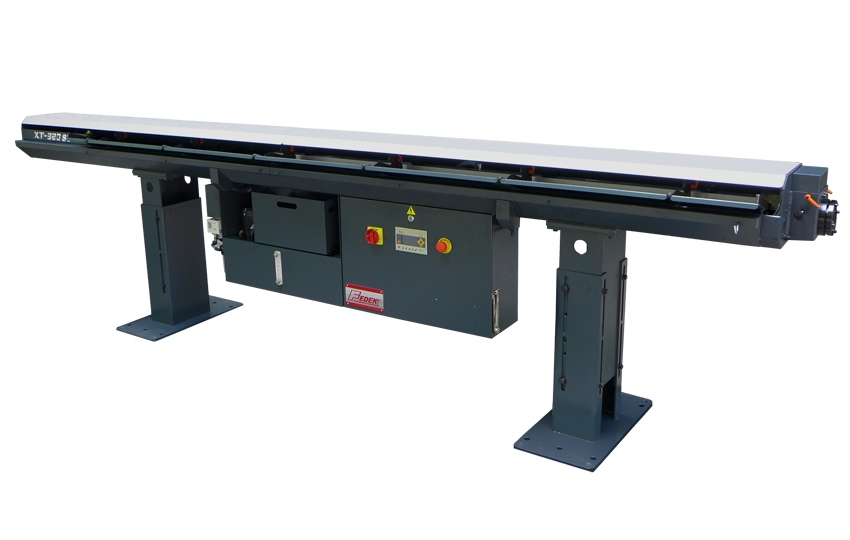
Достоинства барфидеров для токарных станков с ЧПУ
Автоматический податчик прутка значительно упрощает процесс загрузки заготовок, сокращает время установки и позволяет одному оператору обслуживать несколько станков. Чтобы упростить выгрузку готовых изделий, станок дополнительно оснащают уловителем деталей. Это повышает производительность оборудования и делает его работу эффективнее и безопаснее.
Встроенный контроллер делает управление податчиком максимально удобным и экономически выгодным. Для точности подачи заготовок и координации управляющих устройств важно заранее задать корректные установочные параметры.
Интеграция панели управления барфидера с системой ЧПУ токарного станка осуществляется через интерфейсы RS-485. Так можно синхронизировать все процессы и поддерживать стабильную работу оборудования.
Преимущества использования:
- оптимизация работы предприятия за счет цикличной, быстрой и точной подачи заготовок;
- сокращение издержек, снижение затрат на производство;
- повышение качества продукции и производительности труда;
- удаление остатков обработки, уменьшение количества отходов.
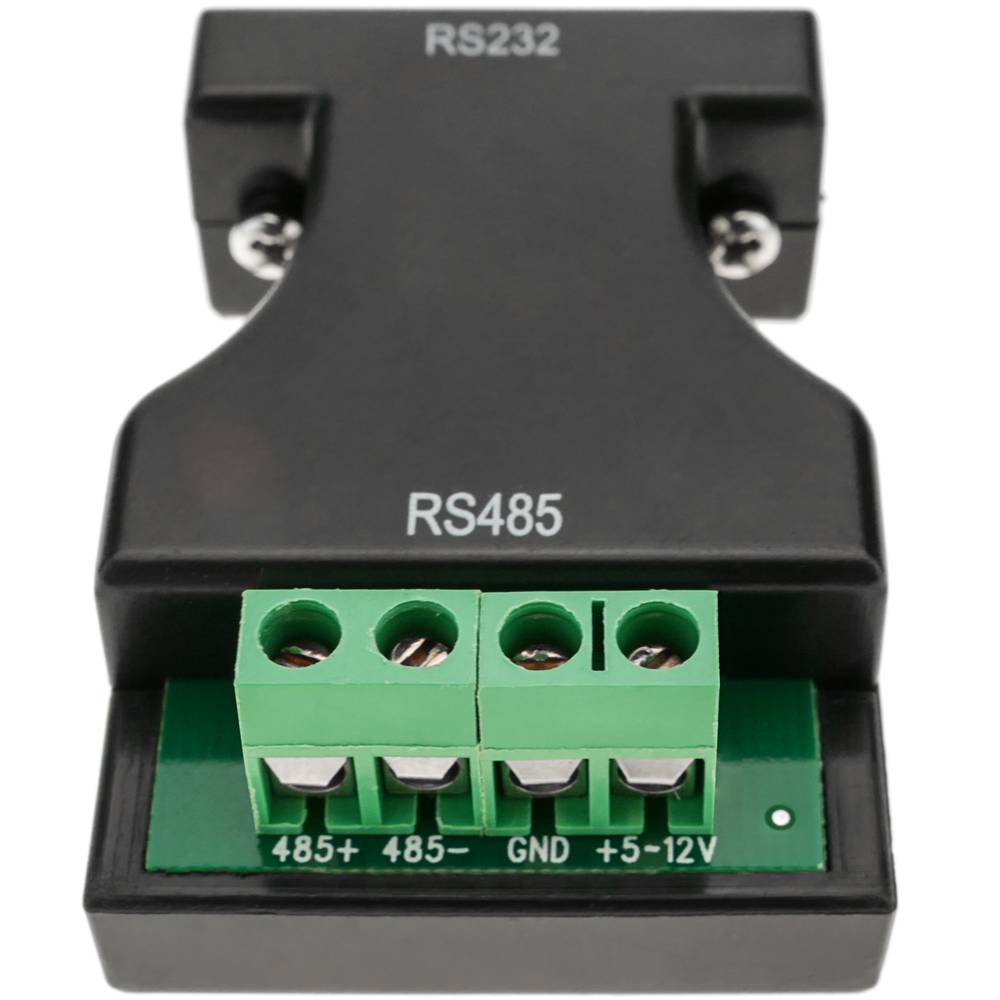
Выгода использования барфидера на токарном станке
Если оператор загружает заготовку вручную, это увеличивает цикл на 20–25 секунд, с помощью можно сэкономить это время и повысить производительность.
Рассмотрим подробный пример, в котором рассчитаем количество готовых изделий с ручной и автоматической подачей. Допустим, общее время обработки одной детали — 5 минут (300 сек). Ручная загрузка в каждом цикле будет дополнительно отнимать 25 секунд: 300 + 25 = 325 сек (5,42 мин).
За 8-часовую смену при ручной загрузке получаем: 480 мин / 5,42 мин ≈ 88 деталей; с автоматической загрузкой: 480 мин / 5 мин = 96 деталей. Разница: 8 штук в смену.
За 22 рабочих дня в месяце выходит:
- без барфидера: 88 × 22 = 1 936 шт;
- с барфидером: 96 × 22 = 2 112 шт.
Дополнительно: 176 изделий в месяц.
За год:
- вручную: 1 936 × 12 = 23 232 шт;
- автоматически: 2 112 × 12 = 25 344 шт.
Если использовать автоподатчик, дополнительно можно изготовить до 2 112 деталей в год.
Чтобы еще больше повысить эффективность производства, рекомендуем доукомплектовать станок ловушкой для деталей. Это может быть обычный лоток для готовых изделий или выходной конвейер, если продукцию нужно транспортировать дальше.
Данные приспособления сократят потерю времени на извлечение деталей, значительно облегчат работу оператора, увеличат производительность на 9 % в смену. Это особенно важно в серийном производстве.
Требования к оборудованию для подключения автоподатчика
Токарный станок должен быть с горизонтальной или наклонной станиной, ось Z — параллельно полу. Барфидер устанавливают соосно со шпинделем по уровню, проводят соответствующие регулировки, настройки и запускают в эксплуатацию. Важно наличие сквозного отверстия в шпинделе для подачи прутка через него.
Для перемещения толкателя используют ременной привод и электродвигатель. Электрический шкаф размещают слева, потому что проводка от барфидера может не дотянуться до другой стороны станка. В противном случае следует предусмотреть удлиненный кабель для подключения.
На станок устанавливают механизированный патрон с обратной связью с ЧПУ, который бывает пневматический, гидравлический или электрический. Главное, чтобы срабатывал датчик давления, зажима, положения тяги и станок получал сигналы при зажатом или разжатом патроне.
Для подъема, запуска загрузчика и смены прутка должен быть предусмотрен подвод воздуха к барфидеру, так как используются пневматические цилиндры.
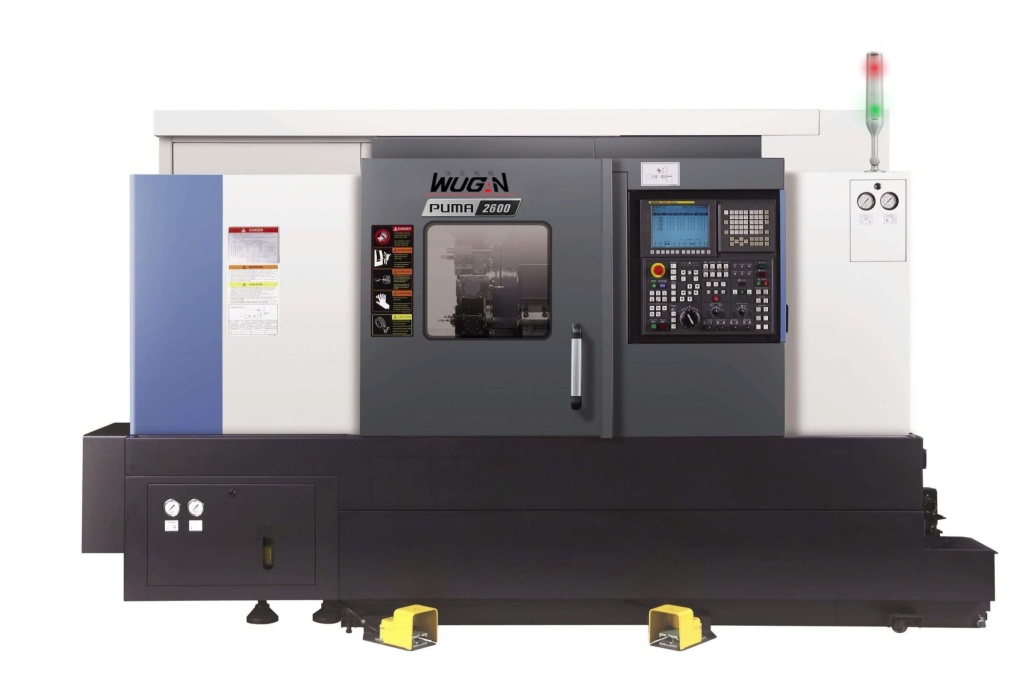
Подводим итоги
Барфидер для токарного станка с ЧПУ своевременно подает заготовку в зону обработки и удаляет ее остаток. Оператору необходимо загружать прутки в накопитель и следить за параметрами программы.
Это довольно дорогостоящее оборудование, но быстро окупается в массовом производстве. Его использование упрощает контроль и управление, способствует эффективному планированию работы, позволяет минимизировать простои и оперативно реагировать на возможные сбои.
Если в станке предусмотрена функция работы с автоматическим податчиком, важно правильно сонастроить их интерфейсы. Если ваш станок не поддерживает такой функции, наши специалисты проведут настройку и совместят его работу с подобранным под ваши задачи подающим устройством. Компания «Техно-СБ» — официальный дилер барфидеров ведущих производителей.