Эту технологию широко применяют в металлургии, приборостроении, микроэлектронике, электротехнике и других отраслях, что увеличивает производительность и повышает качество обработки материалов.
В статье рассмотрим принцип действия лазерной резки, где ее применяют. Расскажем о видах лазерного оборудования, для чего оно предназначено.
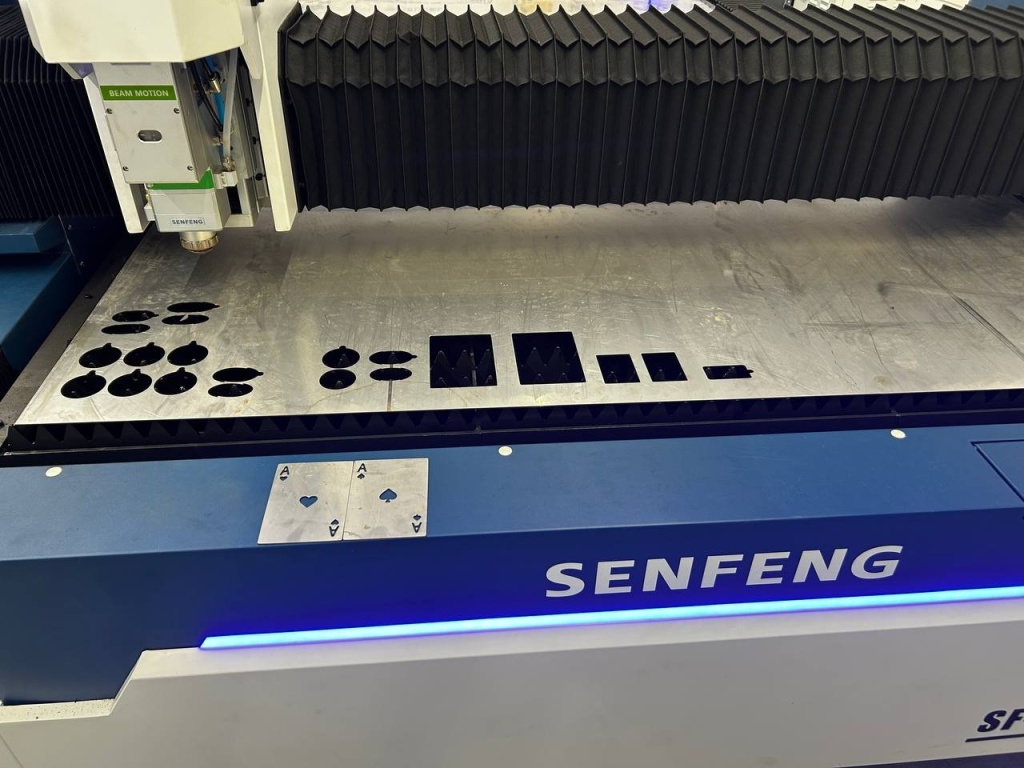
Лазерная резка: что это за технология, когда применяется, каких видов бывает
Лазер используют для изготовления различных деталей и конструкций из листового металла: щитов, панелей, перегородок, кронштейнов. С его помощью создают предметы декора, сувенирную продукцию, металлические изделия сложной формы. Также делают узкие пропилы, гравировку, фигурные и пространственные разрезы, которые невозможно выполнить механическим способом.
В качестве рабочего инструмента применяют лазерный станок ЧПУ. Оборудование оснащено углекислотным или твердотельным оптоволоконным излучателем. Это энергоэффективные современные устройства с высокой точностью обработки, которые способны разрезать практически все виды металлов. Наша команда инженерно-технической службы всегда готова помочь в решении любых проблем, которые могут возникнуть при эксплуатации такого станка.
Суть технологии
Лазерная резка — процесс разрезания металла за счет воздействия сфокусированного лазерного луча на обрабатываемую поверхность. Под действием высоких температур в зоне обработки происходит плавление, кипение и испарение материала. В течение резки все отходы производства улетучиваются. В отличие от механического способа этот процесс очень эффективный, но в то же время достаточно энергозатратный.
В управляющую программу вносят необходимые параметры, по которым резак будет обрабатывать заготовку с оптимальным расходом материала. Пучок излучения фокусируют в нужной точке на поверхности заготовки, где необходимо сделать точный разрез.
Технологический процесс лазерной резки
Состоит из следующих этапов: подготовка металла, настройка станка, выполнение резки.
Сначала металлическую заготовку очищают от загрязнения, пыли, посторонних налипаний, чтобы они не мешали работе станка. Затем проводят необходимые замеры и отмечают траекторию резки. Для точности обработки лист должен быть ровным, при необходимости его выпрямляют.
В автоматизированную управляющую программу загружают необходимые команды ЧПУ и шаблон детали (раскрой). Станок следует по заданному контуру и придает заготовке нужную форму.
В зависимости от толщины заготовки и типа обрабатываемого материала настраивают мощность лазерного излучения, скорость резки, по необходимости проводят дополнительную калибровку оборудования.
Лист устанавливают в рабочем поле станка, направляют по предварительно загруженной управляющей программе рабочий инструмент — лазерную головку, которая подает луч на поверхность металла. Мощное излучение расплавляет металл, пока он не начнет испаряться. Качественный разрез образуется при условии правильно подобранного режима лазерного луча, грамотной юстировки лазерной головы с учетом типа материала и его толщины.
После резки готовое металлическое изделие охлаждают водой или потоком воздуха, чтобы не допустить его деформации.
Существует несколько методов обработки материалов при лазерной резке, среди которых чаще всего выделяют: плавление, горение, испарение, термораскалывание.
Плавление
Это самый распространенный способ обработки металла с помощью лазера, чтобы разрезать наиболее толстые заготовки. В месте среза материал интенсивно нагревают лазерным лучом до температуры плавления. С помощью кислорода поддерживают интенсивность горения; азота, аргона, гелия и других газов — удаляют отходы производства, продукты плавления, охлаждают место разреза.
Газ выбирают с учетом особенностей разрезаемого металла или сплава. Например, для алюминия и нержавеющей стали в большинстве случаев используют азот, для латуни — углекислый газ. Срез получается однородным, с ровными кромками.
Горение
Этот вариант лучше всего подходит для черных металлов. Благодаря интенсивной подаче кислорода к месту среза резко возрастает количество выделяемого тепла, что усиливает действие лазера. Чтобы придать ровность краям, проводят дополнительную обработку изделий.
Испарение
Метод применяют для резки металлических заготовок небольшой толщины. Мощный луч мгновенно нагревает металл до кипения, а образовавшийся пар и отходы производства удаляют напором воздуха или смеси газов.
Термораскалывание
Используют для резки хрупких неметаллических материалов. Под воздействием лазерного излучения в процессе корректировки направления луча происходит контролируемое растрескивание в зоне резки. Данный метод отличается точностью, скоростью и качеством резки по сравнению с другими.
Виды оборудования
Для обработки металлов применяют установки с углекислотным (СО2) и оптоволоконным типом лазера. Каждый вариант имеет свои особенности.
CO2 лазер подходит для листового металла с низким коэффициентом отражения, алюминия, а также нержавейки. Он хорошо режет тонкий профиль, сваривает заготовки, гравирует поверхности. Чтобы усилить мощность луча в процессе резки, используют азот, углекислый или инертный газ. Станки такого типа обладают высокой скоростью и качеством обработки, однако для эффективной работы нуждаются в точном выравнивании.
Волоконные лазерные установки для усиления излучения используют специальные оптические волокна. Они более современные, рассчитаны на многофункциональную обработку листовой стали, меди, латуни, драгоценных металлов и иных материалов с высоким светоотражающим коэффициентом. Благодаря точности и оптимальной скорости резки обеспечивают энергоэффективность производства. Такие устройства могут работать без вспомогательных газов.
Наиболее востребованные лазерные станки с ЧПУ:
- листорезы — резка и раскрой металлических листов различной толщины.
Станок обладает высокой скоростью обработки, эффективно и качественно вырезает изделия с контурами любой сложности. Минимизирует время простоя оборудования, резка становится более надежной и продуктивной.
- труборезы — обработка трубного профиля, металлических труб различного диаметра и формы.
Станки производят раскрой заготовок на части, вырезают отверстия, выполняют фигурный разрез, обрабатывают кромку под сварной шов. Отличаются высокой производительностью. Продвинутые модели оснащены системой погрузки и разгрузки.
- комбинированные (универсальные) — для комплексной обработки, раскроя трубных и листовых металлических заготовок.
Обладают расширенным функционалом, рассчитаны на выполнение широкого спектра задач.
Особенности использования для разных металлов
У разных материалов — различные механические и физико-химические свойства, поэтому при выборе станка важно учитывать их особенности и технологию обработки.
Перечислим ключевые характеристики лазерного оборудования:
- мощность излучения;
- вид лазера;
- скорость обработки;
- толщина листа, габариты обрабатываемой заготовки;
- тип охлаждения;
- дополнительные функции под конкретные задачи.
Для цветных металлов и сплавов мощность лазерного излучения должна быть не менее 1 кВт, для черных металлов — 500–600 Вт. При этом минимальная толщина обрабатываемого листа составляет 0,2 мм, максимальная для разных материалов: алюминий — до 25 мм; медь — до 16 мм; сталь — до 30–40 мм; латунь — до 12 мм.
Заключение
Современное лазерное оборудование с числовым программным управлением эффективно выполняет сложные технологические процессы, высокоточно обрабатывает заготовки практически из любого металла, повышает производительность, сокращает издержки.
В статье рассмотрели основные принципы лазерной резки и виды применяемого оборудования. Чтобы выбрать подходящий станок с оптимальным набором характеристик, обращайтесь к специалистам компании Техно-СБ.